Să vorbim despre rolul cocsului în procesul de furnal. Să aruncăm o privire mai atentă la esența acestei producții metalurgice.
Astăzi, fierul și oțelul sunt fabricate folosind procesul de furnal, în care cuptorul este o componentă importantă.
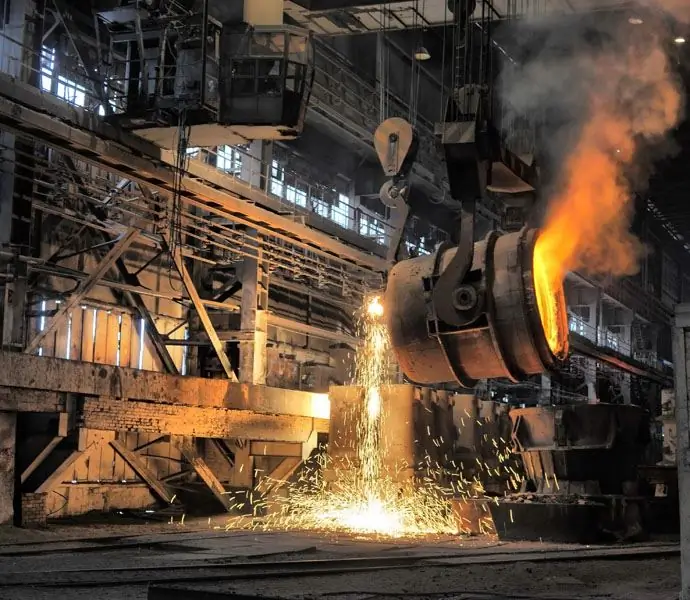
Specificații unității
Luați în considerare caracteristicile dispozitivului, scopul acestuia. Principalele procese ale furnalului sunt asociate cu topirea cocsului. Este un material poros care este sinterizat dintr-o masă de carbon obținută prin calcinarea cărbunelui fără prezența oxigenului atmosferic.
Un furnal este o unitate puternică și de în altă performanță, în care se consumă o cantitate semnificativă de suflare și încărcare.
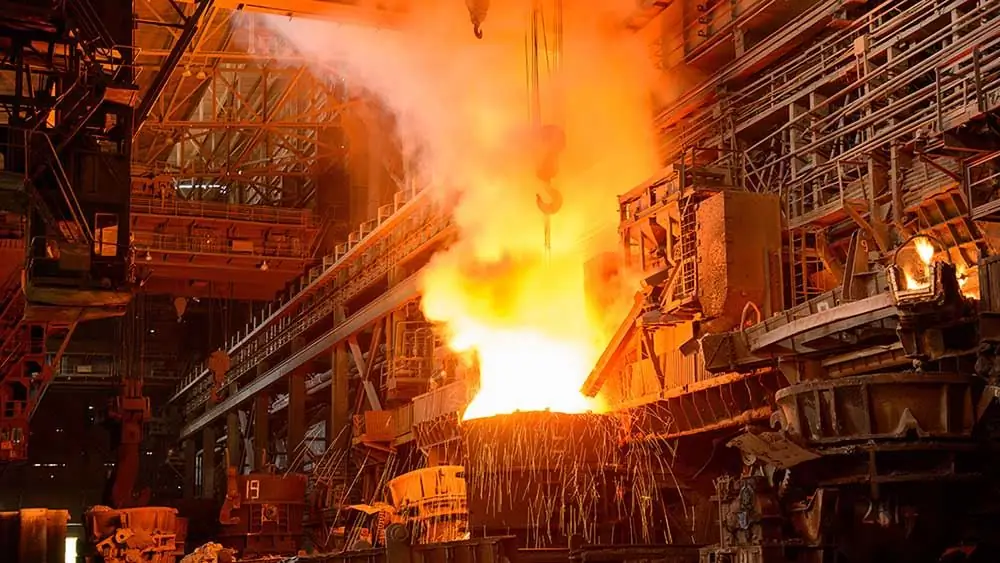
Se încarcă materii prime
Furnalul modern necesită materiale care să stea în el timp de 4-6 ore, substanțe gazoase - 3-12 secunde. Dacă gazele sunt complet distribuite pe secţiune transversalăcuptoare, puteți conta pe rate mari de topire, producția de fier este în curs de desfășurare. Procesul de furnal presupune luarea în considerare a mișcării gazelor prin zone care au o rezistență de încărcare mai mică. Prin urmare, atunci când este încărcat în cuptor, se efectuează reglarea, redistribuirea cocsului și a sinterului pe secțiunea transversală a cuptorului, astfel încât acestea să difere în ceea ce privește permeabilitatea la gaz. În caz contrar, un procent mai mare de gaze va părăsi cuptorul cu o temperatură semnificativă, ceea ce va afecta negativ utilizarea energiei termice, procesul de furnal nu va fi pe deplin eficient.
În acele zone care au rezistență mare, amestecul de gaz va trece ușor încălzit, va fi nevoie de căldură suplimentară în partea inferioară a cuptorului, ca urmare, consumul de materii prime va crește semnificativ.
Ce alte funcții sunt importante de luat în considerare la descărcare? Procesul de furnal pentru producerea fontei este o producție consumatoare de energie. De aceea, în apropierea pereților cuptorului se folosește un strat de aglomerat mai puțin permeabil la gaz, iar în centru se crește un strat de cocs, datorită căruia fluxul de gaz este redistribuit în centru. Materialele sunt distanțate uniform în jurul circumferinței.
Taxa este încărcată în porțiuni separate - fluxuri. O porțiune constă din mai multe skip-uri, parte de minereu (aglomerat), cocs. Raportul dintre ingredientele originale este determinat de experți.
Procedeul în furnal permite co-alimentarea cu materii prime, în care cocsurile și skiturile de sinterizare sunt colectate pe un con mare și apoi încărcate într-un cuptor.
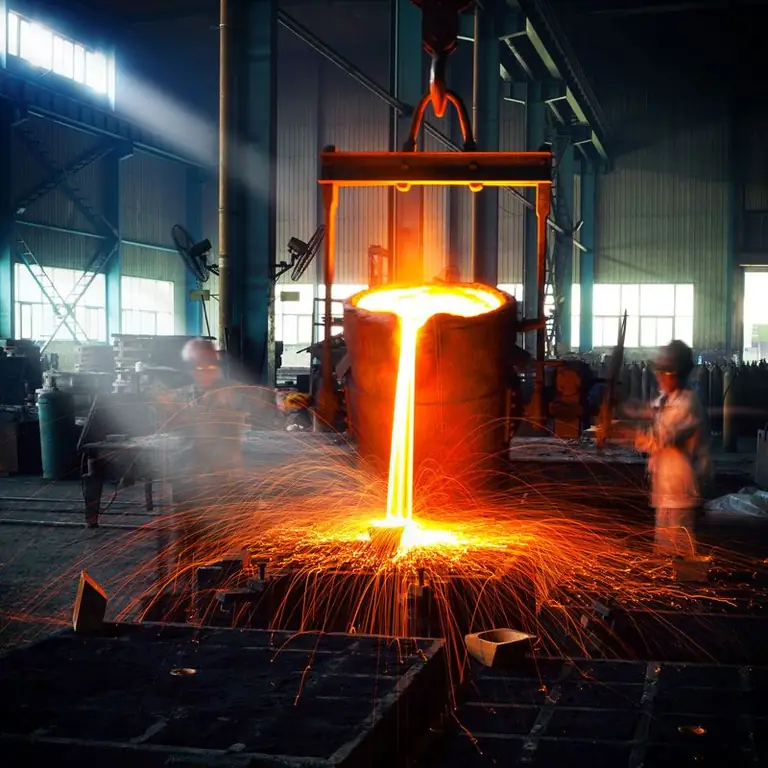
Ajustarea distribuției lotului
Distribuția cocsului și a aglomeratului pe secțiunea transversală a blaturilor este controlată prin următoarele metode:
- schimbarea ordinii materiilor prime pe conul mare;
- Se aplicăporții împărțite și împărțite;
- plăci mobile sunt instalate lângă pereții din partea superioară.
Procedeul furnalului presupune luarea în considerare a anumitor regularități pentru introducerea materialelor vrac:
- așezarea materiilor prime care cad dintr-un con mare pe un vârf cu o înălțime - un pieptene;
- La creasta (în punctul de cădere) a încărcăturii se acumulează fine, bucăți mari se rostogolesc până la piciorul crestei, prin urmare, în această zonă, permeabilitatea la gaz a încărcăturii este mai mare;
- cresta este afectată de nivelul de umplere din partea de sus, precum și de distanța cu un con mare;
- conul mare nu coboară complet, așa că bucăți mici de coca ajung la periferie.
În cea mai mare parte, centrul cuptorului primește material din skiturile de alimentare, care au fost ultimele care au fost încărcate în conul mare. Dacă modificați ordinea de încărcare, puteți obține o redistribuire a materialelor pe secțiunea transversală a vârfului.
Pentru a controla procesul de distribuție a încărcăturii utilizate pe volumul cuptorului, se folosesc două aparate cu conuri. Recent, unele furnale sunt echipate cu plăci mobile lângă pereții vârfului, permițându-vă să schimbați unghiul de înclinare, să le mutați de-a lungul unui plan orizontal.
Bucăți din sarcina care cad pe plăci sunt reflectate din ele, ceea ce vă permite să direcționați materia primă către anumite zone ale vârfului.
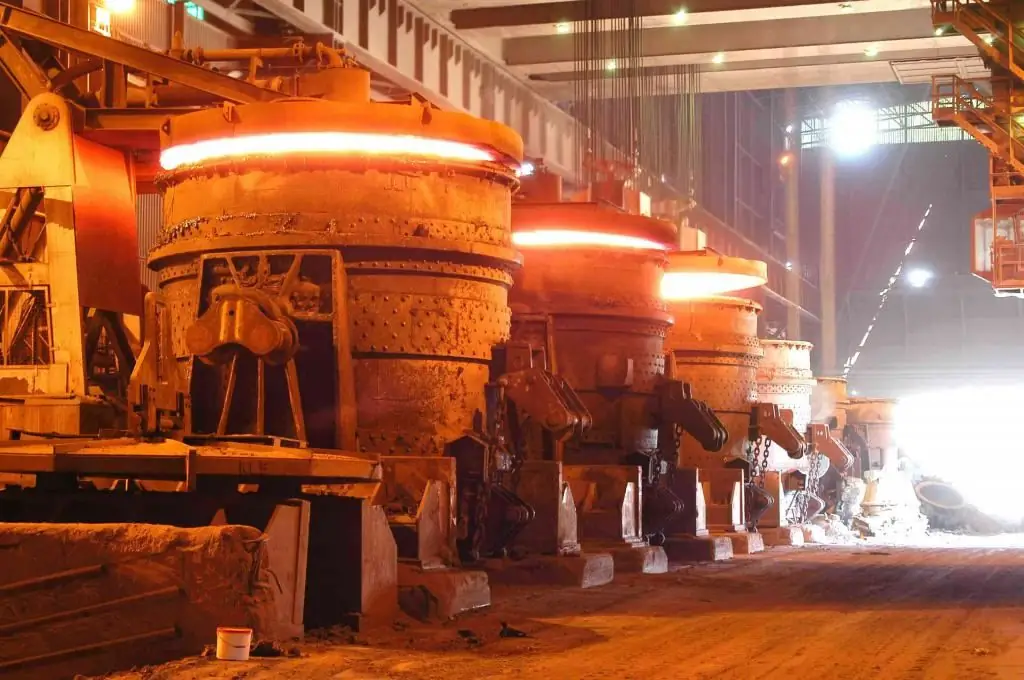
Opțiuni pentru aragazfără conicitate
La cuptoarele care nu au dispozitiv de încărcare conică, încărcarea materiilor prime se realizează prin două buncăre de ecluză care se deschid alternativ. Materiile prime le sunt livrate prin transportoare cu bandă înclinată, pe care cocs-ul și sinterizarea sunt amplasate la intervale clare. O porțiune vine de la centură într-un buncăr, apoi este descărcată pe partea superioară a cuptorului de-a lungul unei tăvi înclinate rotative. În timpul perioadei de descărcare, fac aproximativ zece rotații complete în jurul axei centrale fixe.
Cicl de încărcare
Se obișnuiește să se numească un număr repetat de loturi de materiale de încărcare. Porțiunea maximă este determinată de volumul buncărului de blocare al mecanismului de încărcare. Numărul de porții într-un ciclu poate fi de la 5 la 14. Cum să obțineți produsele din procesul de furnal în întregime? Pentru a răspunde la această întrebare, să aruncăm o privire mai atentă la esența procesului. Cu un conținut crescut de dioxid de carbon în amestec, temperatura scăzută contribuie la completarea schimbului de căldură și a proceselor chimice în furnal. Pentru ca aparatul să funcționeze economic și intensiv, conținutul cantitativ de dioxid de carbon de-a lungul axei și la periferia cuptorului ar trebui să fie redus, iar la o înălțime de unul sau doi metri de pereți - crescut.
Controlul temperaturii în cuptoarele noi se realizează prin introducerea de sonde prin orificiile din carcasă. Obligatoriu pentru toate procesele este controlul nivelului de umplere din partea de sus.
Printre inovații se numără utilizarea metodelor de măsurare a nivelului fără contact bazate pe citirile senzorilor cu microunde și infraroșu.
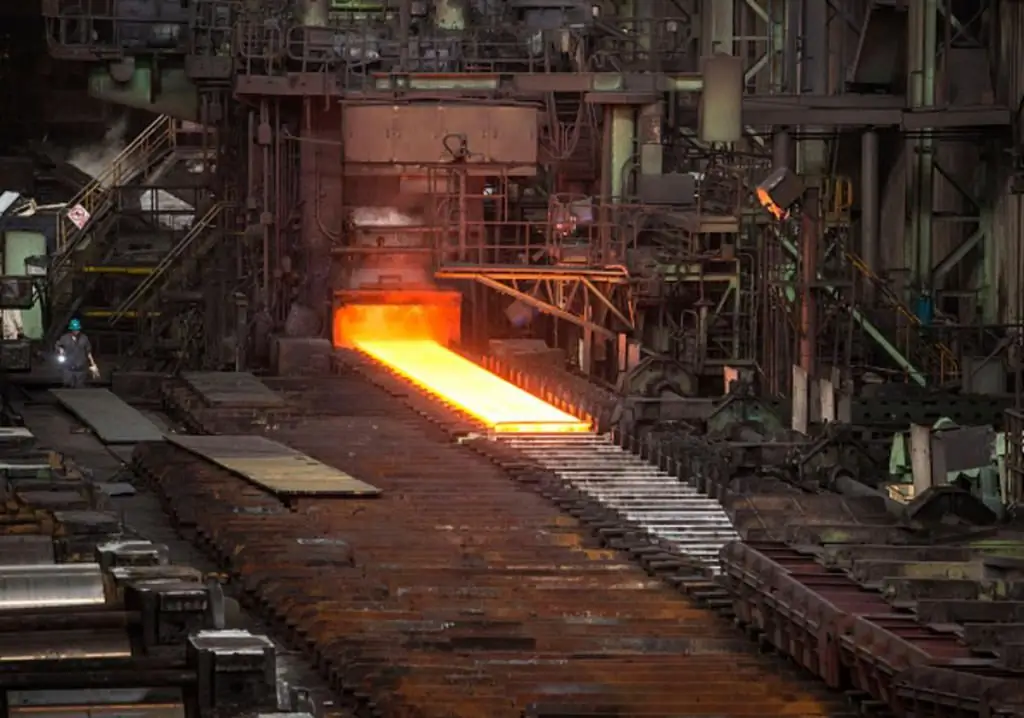
Funcții de distribuție a temperaturii
Pe lângă căldura care este introdusă prin explozie încălzită, ca principală sursă de căldură pentru încălzirea gazelor și a încărcăturii, realizând recuperarea și compensarea pierderilor de căldură, este posibilă compensarea pierderilor cu căldura care este degajată în timpul arderii combustibilului în partea superioară a focarului. Pe măsură ce produsele gazoase se deplasează în sus din vatră, căldura coboară către materialele reci de încărcare și are loc schimbul de căldură. Un proces similar explică scăderea temperaturii de la 1400 la 200 de grade la ieșirea din partea superioară a cuptorului.
Elimina excesul de umiditate
Să luăm în considerare principalele procese fizice și chimice dintr-un furnal. În încărcătura, care este încărcată în furnal, există umiditate higroscopică. De exemplu, în compoziția cocsului, conținutul acestuia poate fi de până la cinci procente. Umiditatea se evaporă rapid deasupra, așa că este nevoie de căldură suplimentară pentru a o îndepărta.
Umiditatea hidratată apare atunci când minereul de fier brun și caolinul sunt încărcate în furnal. Pentru a rezolva problema producției moderne de fier, aceste minereuri practic nu sunt folosite ca materii prime.
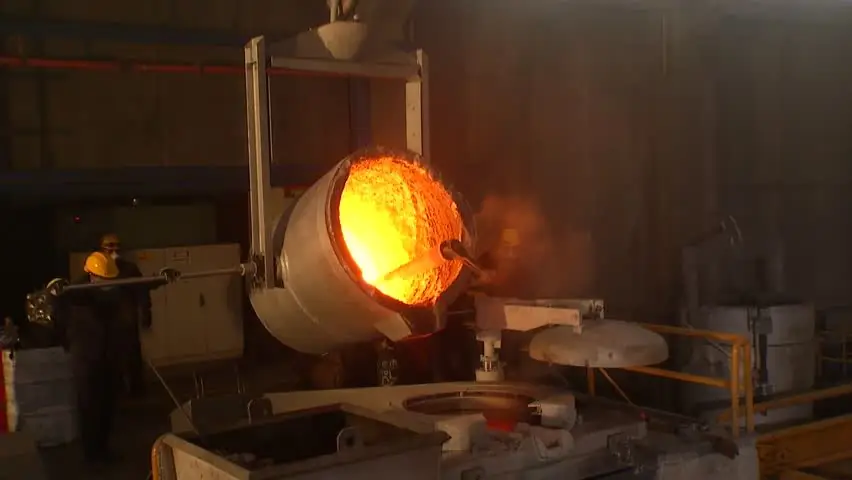
Procese de descompunere a carbonaților
Sărurile acidului carbonic pot intra în furnal. Pe măsură ce se încălzesc, se descompun în oxizi de calciu și carbon, iar procesul este însoțit de eliberarea unei cantități suficiente de energie.
Recent, aproape niciun minereu nu a fost încărcat în furnalele în alte. Care este rolul fluxurilor în procesul de furnal? Îi sporesc eficacitateapermit reducerea costurilor de producție. Datorită utilizării sinterului fluxat, îndepărtarea completă a calcarului din încărcătura furnalului poate realiza economii semnificative de cocs. Procesul de descompunere a calcarului în timpul aglomerării este asigurat de arderea combustibilului de calitate scăzută.
Recuperarea fierului
Fierul este introdus în furnal sub formă de oxizi. Obiectivul principal al procesului este de a maximiza extracția fierului din oxizi prin reducere. Esența procesului este de a elimina oxigenul, carbonul, monoxidul de carbon, hidrogenul sunt utilizați pentru aceasta. Reducerea cu carbon se numește proces direct, iar reacția cu substanțele gazoase se numește interacțiune indirectă. Care sunt caracteristicile lor distinctive? În reacția directă, carbonul este consumat, în urma căruia cantitatea acestuia este redusă semnificativ. Al doilea tip de reducere a fierului din oxizi necesită o cantitate în exces de hidrogen.
Procedeul produce fier solid. Gradul de recuperare în fontă este de 99,8%. Astfel, doar 0,2 -1% se transformă în zgură.
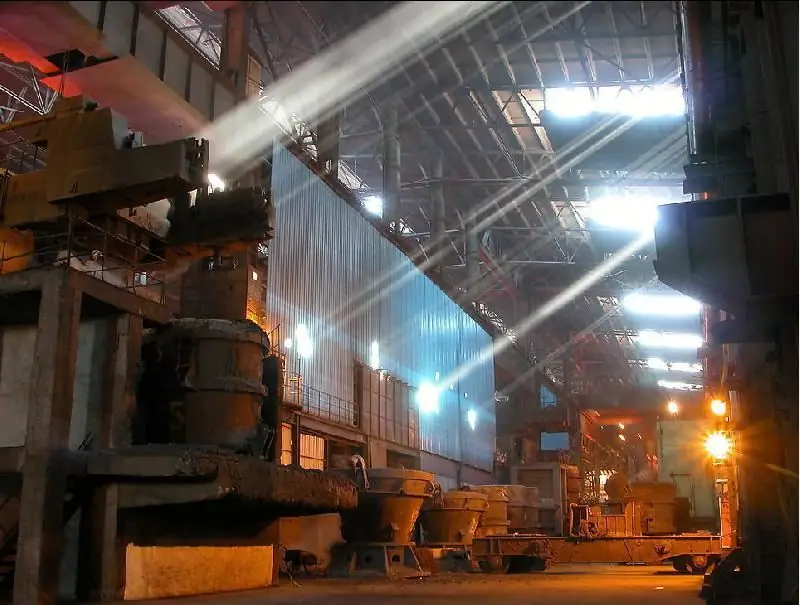
Topirea fontei de mangan
În procesul de topire a fontei remanufacturate, manganul intră în furnal sub formă de aglomerat. În unele cantități, minereurile de mangan sub formă de silicați de mangan contribuie la producerea fontei de mangan.
Recuperarea de la oxizii de mangan are loc în etape. Pentru a finaliza procesul, trebuie setate temperaturi ridicate în cuptor. Procesul de topire a fontei este însoțit dereducerea manganului numai în proporție de 55-65%. În prezent, din cauza deficitului de minereuri de mangan și mangan, o cantitate mică de fontă de mangan a fost folosită în lanțul tehnologic. Când treceți la fontă cu conținut scăzut de mangan, este posibil să economisiți nu numai manganul în sine, ci și cocs, deoarece consumul acestuia pentru reducerea directă a metalului va scădea.
Concluzie
Procedeul furnalului este una dintre principalele metode de topire a fierului și a oțelului. În funcție de ce componente sunt introduse în amestecul inițial, în prezent se obțin diferite tipuri de produs finit. Dintre domeniile de aplicare ale fontei și oțelului rezultat, evidențiem: inginerie mecanică, industria chimică, medicină, fabricarea instrumentelor.